版权声明:本文内容由互联网用户自发贡献,该文观点仅代表作者本人。本站仅提供信息存储空间服务,不拥有所有权,不承担相关法律责任。如发现本站有涉嫌抄袭侵权/违法违规的内容, 举报,一经查实,本站将立刻删除。如若转载,请注明出处:http://ti8.net/_chao__bin__/8586.html
定制报告-个性化定制-按需专项定制研究报告
行业报告、薪酬报告
联系:400-6363-638
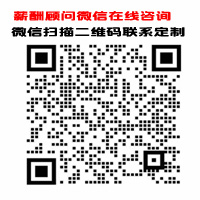
《西门子数字化工业软件:2024年Simcenter电驱动系统性能开发白皮书(51页).pdf》由会员分享,可在线阅读,更多相关《西门子数字化工业软件:2024年Simcenter电驱动系统性能开发白皮书(51页).pdf(51页珍藏版)》请在本站上搜索。 1、西门子数字化工业软件Simcenter电驱动系统性能开发白皮书内容摘要本白皮书讨论了混合动力和电动汽车行业中电驱动系统端到端设计流程的工程、仿真和分析挑战。针对典型的“V”字形设计流程,从概念设计到原型机生产的每一个阶段都进行了讨论。电驱系统主要的工程化目标包括高功率密度、高效率、高可靠性和低成本。使用现代仿真工具进行新颖的集成设计和开发工作流程将在实现这些目标方面发挥核心作用。在本白皮书中,我们讨论了先进的 Simcenter 软件工具套件的核心优势,以及如何使用这些工具来应对当前和未来的电驱动系统设计挑战。提 供 集 成 的 工 具 和 方 法 以 应 对 未 来 的 挑 战https:/2、 Simcenter电驱动系统性能开发目录电驱市场预测 3电驱开发中的工程挑战 5Simcenter电驱动系统解决方案 7电驱系统架构创成设计及评估8电驱系统设计目标确立11电机选型及设计迭代13电机电磁性能仿真验证及优化15电驱结构多物理场仿真分析18电驱散热性能分析22电控系统散热分析25电驱动系统性能集成化分析28电控系统策略开发与在环验证33电驱系统振动噪声及疲劳试验验证36电驱系统基于模型的系统测试39Simcenter产品组合介绍41总结 49 2西门子数字化工业软件白皮书 Simcenter电驱动系统性能开发交通运输行业正在迅速转型,这主要是由车辆电气化、自动驾驶的发展、工业4.3、0技术的应用、不断变化的消费者数据、经济和环境可持续性问题等推动的。其中一些趋势源于尽量减少温室气体排放水平,开发更安全的运输方式,降低运营成本并提供更好的产品生命周期管理系统。在众多变化中,电气化受到的关注最多。市场趋势预测,未来几十年对内燃机汽车替代品的需求(图1)将迅速增长。全球大部分地区设定了雄心勃勃的目标,即在2030年至2050年期间逐步停止内燃机汽车的销售。电驱市场预测这些趋势对混合动力和电动汽车行业的所有细分市场都有广泛的影响,包括动力系统零部件制造商、供应商和集成商。混合动力和电动汽车的动力系统的主要部件是电池或燃料电池、驱动电机、电力电子系统和传动系统。在本白皮书中,我们从4、行业趋势、挑战和解决方案的角度分析了电驱动设计的现状和未来方向。其中一些关键问题包括:开发新的和改进的电驱动的需求是否会随着行业的整体增长而增长 下一代电驱动设计工程师面临的技术挑战和机遇是什么 有哪些关键的计算和仿真解决方案可以帮助当今的设计人员应对未来的工程挑战图1内燃机汽车、混合动力和电动汽车的相对需求 3西门子数字化工业软件白皮书 Simcenter电驱动系统性能开发下面我们将逐一围绕这些问题展开讨论。首先,我们介绍了电驱动设计开发人员面临的一些主要工程挑战。然后,结合典型的电驱动V字型开发流程,介绍了在每个步骤中的关键设计任务,包括使用仿真工具执行这些任务所需的功能,以及西门子Sim5、center软件解决方案。最后,我们讨论了采用由本文介绍的一些工具实现的集成设计过程的优势。4西门子数字化工业软件白皮书 Simcenter电驱动系统性能开发工程中所面临的一个重要方面是目前的电驱动无法满足未来纯电动和混合动力汽车的技术标准和性能要求。包括效率水平、功率密度、速度范围、生命周期成本和其他方面都达不到下一代电驱设备所需的水平。这给主机厂和其他利益相关者带来了机遇和挑战。虽然本白皮书的主要重点是技术挑战,但值得从一个对电驱动行业产生巨大影响的非技术问题开始稀土材料的供应和价格波动。这些材料用于制造高强度永磁体,并用于许多商用电动和混合动力汽车(丰田普锐斯,日产聆风,宝马i3,特斯拉6、Model3等)驱动电机。稀土材料的供应问题导致了巨大的研发投入,以开发不使用稀土永磁体或减少使用稀土永磁体的电机替代品。自2012年以来,这个问题持续占据大部分围绕下一代电驱动开发的讨论。因此,我们认为开发不使用或减少使用稀土永磁体的高功率密度驱动电机是下一代设计师面临的主要挑战之一。另一个重要挑战是开发高效电机。为了应对气候变化和不断增长的人口对能源的需求,世界各国政府已强制要求降低车辆的排放水平。这反过来又增加了对高效电机的需求。考虑到大多数驱动电机目前以大约90%的效率运行,开发更高效的电机是一个很有挑战的问题。要改进这一点,需要结合材料工程、稳健性设计、制造工艺(例如,使用增材制造)7、和仿真技术的新技术进步。对于给定的电池,电驱动系统只能在某个转速下运行,该速度由其恒定功率与(基本)速比确定。这是影响电机类型、材料、齿轮传动比和其他动力总成细节选择的重要制约因素。大多数现代电机的恒功率转速范围约为2.5至4,将此范围扩展到7到10是未来机器的目标之一。如果可行,这将有助于大幅降低动力总成传动系统的成本。通过确保稳健性来降低成本是所有机器的另一个重要目标。稳健性的要素包括在制造不确定性和公差下保持机器性能,防止系统故障,确保在可变环境条件下运行的能力等。仿真软件工具是确保机器稳健性的重要推动因素。降低电驱动系统的噪音和振动(NVH)水平是另一项重大技术挑战。由于转子偏心、脉宽8、调制(PWM)的控制策略或者其他原因引起的谐波激励产生的NVH问题是难以避免的。此外,除了技术挑战外,对于整个产品研发周期的缩短以及产品多样化的需求也给电驱开发带来的巨大的挑战。面对这些问题,我们需要更加高效地利用仿真方法和工具实现电驱动系统的正向开发。电磁设计是电驱动系统设计仿真的重要部分。除了电磁设计外,电驱动设计还有其他几个方面:传动系统设计,散热或冷却系统设计,电力电子或驱动设计,符合NVH标准并保持机器的结构完整性,以及各种子系统和组件的系统级集成。冷却系统的设计需要电磁-热耦合仿真。为此,需要基于各种保真度级别的模型来进行电磁热耦合仿真,从集总参数到基于计算流体动力学(CFD)的计9、算。对于电力电子驱动,需要耦合电磁和功率器件仿真。结构分析和NVH仿真需要结构和电磁场进行耦合。对于系统级设计,需要高保真度级别的模型。其中每一项都带来了重大挑战。例如,在电磁、热和机械仿真工具之间进行有限元分析的仿真时,时间常数和网格要求的差异只是必须考虑的众多方面中的一部分。此外,基于CFD的仿真的计算成本可能会使某些问题在不使用高性能计算功能的情况下无法解决。电驱的设计空间是高维的。此外,当考虑到问题的多学科和多物理场时,设计目标和约束的数量通常也很高,这导致许多优化方法无效。面对众多选择,工程师面临的一个重要挑战是为原型设计选择优化设计候选方案。利用最先进的流程集成和多目标优化算法可能10、会有所帮助。这是一个广阔的研究领域,应用新的技术创新对软件工具开发人员来说既是挑战也是机遇。当非线性很重要时,实验设计和优化问题通常需要使用计算量大的基于有限元的分析方法来建模求解,这些模拟可能很耗时。根据手头的问题,可能需要数千次评估。在这些情况下,必须执行基于降阶模型的性能预测。开发高保真降阶模型是一项重要的算法挑战。电驱开发中的工程挑战 5西门子数字化工业软件白皮书 Simcenter电驱动系统性能开发最后的建模挑战与创建全面的数字孪生有关。在本文中,我们将电驱动系统的数字孪生称为它们以各种形式集成化表征的模型。等效电路或集总参数表示、低阶或降阶模型、响应面模型和基于有限元的模型都是机器11、数字孪生的示例。就目前而言,集成化电驱动系统模型可以实时更新,并允许在不同仿真平台之间进行无缝模型交换,以进行多物理场和多领域分析。在上面的讨论中,我们总结了当今电驱动设计开发人员面临的一些最重要的工程、仿真和分析挑战。仿真工具将在应对和克服这些挑战方面发挥核心作用。在下面章节中,我们将更深入地介绍在电驱开发设计过程,西门子Simcenter所提供的解决方案。6西门子数字化工业软件白皮书 Simcenter电驱动系统性能开发电驱动系统开发如下图2所示,涉及到诸多设计、验证及其相互迭代的过程。通常来讲,一个正向研发过程首先从整车需求指标分解开始,明确电驱动系统的各部件的设计目标,然后进行部件级详12、细设计,其中包括:电磁方案以及动力性能设计、传动方案设计、电驱动系统散热设计及热管理策略开发、电驱动系统的NVH设计及优化等。待各部件性能开发完毕,工程师利用多学科系统仿真平台将表征电驱动系统各项性能的模型进行集成,同时完成整车层面的设计指标验证。在这个过程中,工程师需要不断对各部件的详细设计进行局部优化调整,以此使整车综合性能表现达到平衡。与此同时,为缩短产品研发周期,控制工程师利用前期建立的电驱动系统部件级模型开始控制策略的虚拟标定工作,包括:以能耗最低为目标的基波电流幅值相位标定、以输出扭矩波动最小为目标的谐波注入电流幅值相位标定等。上述性能开发工作完成后,电驱动系统研发进入样件试制阶段13、。软件工程完成控制策略的程序实现、硬件电路完成制版、元件焊接与基本功能调试、电机本体生产制造完成并与电驱动系统一体化集成结构完成装配。测试阶段根据实际验证工作需要,依次完成软件在环测试、硬件在环测试、台架测试与实车测试。工程师借助于开发阶段所搭建的系统或部件级详细模型,完成电驱动系统虚实结合的测试过程。在此过程中,数字孪生中的实物部分将逐渐替代虚拟模型部分,从而使测试环境越来越接近于系统真实运行环境。借助于数字孪生技术,电驱动系统的开发周期大幅度缩短,同时得益于虚拟仿真技术的应用,使得设计缺陷尽可能地暴露在早期验证阶段,从而大大降低了电驱动系统的研发成本。在以下各节中,我们将从设计和性能开发工14、程师的角度讨论所需的仿真工具功能。在设计过程的每个阶段,我们将介绍Simcenter解决方案如何提供可帮助您应对上述挑战的功能。Simcenter电驱动系统解决方案图2电驱动系统性能开发与测试验证 7西门子数字化工业软件白皮书 Simcenter电驱动系统性能开发电驱系统架构差异是系统性能差异关键所在,不同系统架构对于所设计产品的成本、性能之间的差异起着决定性的作用,不同驱动方式形式的续航里程、系统可靠性也会有本质的差别,组成更少的集中式电驱系统更容易获得更高的可靠性,轮边电机或者轮毂电机式驱动方式的电动汽车具有更高的加速性能,但同时成本也会更高,这些重要性能的决定因素就是系统架构。不同架构的15、总体系统设计也决定着子系统与零部件的设计,例如不同的驱动形式决定着不同的电驱动系统的拓扑结构,因此合理的系统架构规划有利于充分利用电动车/混动车的零部件特点和整车总体优势,例如成员舱空间、车身碰撞性能、更好的整车尺寸等,此外对于零部件选型和设计也有很强指导意义。在汽车设计概念阶段,工程师通常根据直觉或以往设计经验进行总体架构方案设计和整车性能指标决策,这将导致设计固化从而限制架构方案的创新和寻求优化方案的可能性,整车性能参数被设定后由下游开发团队进行子系统性能标定,随着越来越多的关键指标的确定,设计固化的问题也越来越明显,一旦一种或局限的几种架构方案被设定,我们可以通过仿真进行设计优化,但此时16、已为时已晚,我们无法获悉是否存在更好的架构方案。面对上述问题,我们需要一个能够帮助工程师进行快速的架构方案创成和评估的工具来进行xEV架构和配置方案的探索和寻优,SimcenterStudio是Simcenter产品组合中的一个应用,用于在早期概念阶段生成和评估系统架构。该软件包含有专利技术,以便使工程师和数据科学家创建新颖的、拓扑上不同的系统架构。SimcenterStudio还将系统仿真、控制方法、以及建立在最先进的机器学习和科学计算堆栈之上强化学习合并在一起,以便对数百种此类架构进行自动仿真和评估。这种方法允许工程师和数据科学家在计算笔记本中创建用户定义的程序,用于创成式工程。电驱系统架17、构创成设计及评估SimcenterStudio可以基于用户定义的系统组成、接口数量与类型等生产各种可能的系统架构和配置方案,SimcenterStudio与Amesim联合仿真获得各个需要评估的性能参数。Studio将Amesim中的仿真结果存储于HDF5文件中,同时对结果数据进行后处理并可视化,形成包含了所有的架构、不同架构各参数分部图、各种性能的统计结果,我们通过性能的选择,可以获得满足要求的系统架构。图3SimcenterStudio架构创成工作和评估流程 8西门子数字化工业软件白皮书 Simcenter电驱动系统性能开发图4电驱系统可能的架构数量图5SimcenterStudio自动生18、成拓扑架构和配置方案以电驱系统为例,基于SimcenterStudio进行架构的设计,首先基于功能分析建立电池、电机、变速器、传动系统与车辆等;SimcenterStudio中可以对组件的数量进行控制,例如我们可以选择1个、2个、3个或4个电机对汽车进行驱动,采用0或者1个齿轮箱来构建系统。根据工程经验,可以设置某个接口必须与另外一个接口相连接或无法连接的限制连接或者指定连接条件,从而生成符合要求的系统架构。同时,SimcenterStudio可以设置各个组件的变体参数,例如电机功率和扭矩为96Kw,250Nm或50Kw,200Nm,减速器速比等等。基于上面设置的限制条件与组成设置、接口设置要19、求,SimcenterStudio基于AI技术最终可以自动生成满足条件的所有系统架构和配置方案。9西门子数字化工业软件白皮书 Simcenter电驱动系统性能开发Studio通过调用Amesim仿真计算可以获得各种架构和配置方案下汽车百公里加速时间,这是汽车动力性能评估主要的指标之一。Studio生成除了百公里加速外,其他如能耗、里程等方面的计算结果,结果中包含了所有的架构、不同架构各参数分部图、各种性能的柱状统计结果,我们通过性能的选择,可以获得满足要求的系统架构。图6不同架构所获得的百公里加速时间及能耗结果 10西门子数字化工业软件白皮书 Simcenter电驱动系统性能开发电动汽车设计初20、始阶段,根据市场需求调研、用户反馈和对标车型的性能参数、工程师已经拿到待研发车型的整车级动力性、经济性指标,例如:标准法规循环工况下的续航里程,百公里加速时间、超车加速时间、最高车速、最大爬坡度等。如何根据这些整车级的性能指标来定义电驱动系统的部件性能,是整车性能工程师面临的首要问题。这些部件的性能指标既包含了动力方面,同时还包含NVH以及散热方面。电驱系统设计目标确立图7整车需求分解与部件设计目标确立我们寻求根据车辆类别、典型驱动循环和约束、车辆性能指标等来推导出要设计的电驱系统的目标性能。在此阶段,将执行系统级分析,在分析中组件尺寸和配置以及传动系统拓扑可能会发生变化。结果用于确定所需的电21、机性能特性。这些特性可能包括峰值和连续工作模式下的功率、速度范围、效率水平等。从软件角度来看,需要一个快速的1D系统仿真工具来考虑多种xEV动力总成配置和组件尺寸变化。对于电机部件,需要不同电机类型的速度-扭矩-效率图来计算到车轮的效率和其他性能参数,如能耗、加速时间、车辆续航里程和爬坡能力。除了效率图变化外,还可以研究改变电池类型和尺寸、逆变器/转换器开关策略、开关损耗、电流或功率限制、单速或多速传输、冷却方法、NVH特性和再生制动模式模拟的影响。最终,系统级仿真工具将促进不同电机类型、传动系配置、电力电子仿真和齿轮配置的模型参数化。系统级仿真的实用性不仅限于尺寸调整,它可以在设计的所有阶段22、用于评估器件性能,以进行热、NVH和/或其他分析。从驱动电机设计的角度来看,至关重要的是该工具不会将设计人员限制在任何特定的电机类型或配置上,并且可以不受限制地进行设计探索。例如,对于驱动电机设计,希望能够缩放电机的效率图。同时,设计人员应该能够考虑温度对电机输出的影响。这些是系统级仿真软件在设计过程的迭代阶段为牵引电机设计所期望的一些重要功能。SimcenterAmesim软件专为应对这些挑战而设计。它是多领域、多物理系统一维仿真的行业领导者。通过与Simcenter电机设计和其他特定领域的多物理场工具紧密结合,它使设计人员和分析人员能够在开发过程的任何阶段评估设计迭代的影响并优化其设计。最23、强大的方面之一是内置功能,用于在多个保真度级别表示可扩展的牵引电机模型。11西门子数字化工业软件白皮书 Simcenter电驱动系统性能开发SimcenterAmesim中电机表示的各种保真度级别包括线性化、完全非线性和温度相关的模型。这些模型用于驱动设计、热系统设计、NVH特性评估,并最终用于创建全面的数字孪生。以满足整车动力性的部件设计指标的确立为例进行说明。根据整车的动力性经济性需求,需要明确的部件参数包括:电机峰值/额定扭矩、峰值/额定功率、最高转速、额定转速,减速比等。工程师可以借助SimcneterAmesim系统仿真平台搭建整车性能仿真模型,该模型包括了电机、减速器、电池包、VC24、U、驾驶员、整车等电驱动系统及其相关系统的关键部件。通过预设电机的外特性参数、电驱动系统效率、减速比、电池单体容量以及成组方式,可以轻松获得整车的动力性和经济性表现。图8基于模型的整车级需求分解与验证在此基础上工程师根据现有不同产品选型,对满足整车级指标需求的多方案设计进行综合分析和优化,例如以电驱动系统的总体效率、动力性能输出为评价依据,综合考虑电机外特性参数与减速比的匹配性设计,从而确定满足系统级指标的最合适部件性能组合。12西门子数字化工业软件白皮书 Simcenter电驱动系统性能开发在确定给定应用所需的电机外特性后,开始进行电机初始化设计,然后进行迭代。这是概念开发过程的主要步骤之一25、。在此期间,寻求可行的设计或满足上一步得出的目标性能标准的几个候选设计。除了获得满足性能目标的候选设计外,确保最终设计与适当的冷却系统兼容,并能在各种负载条件下保持结构完整性也很重要。此阶段的关键步骤是设计初始化、材料选择、绕组模式选择和几何形状的微调。从软件工具的角度来看,需要许多重要的功能。首先,在此阶段,快速获得结果和性能计算至关重要。通过不同的电机拓扑结构、绕组配置和材料来探索设计只是寻找可能候选者的众多参数中的一小部分。需要快速评估以了解这些变化对电机性能的影响。这意味着与探索各种选项相关的计算规模必须是最小的。理想情况下,在此阶段需要使用模板化的快速(解析或半解析)计算方法。其次,26、必须具有创新的灵活性。正在为下一代高功率密度电机探索的一些最有潜力的设计选项是基于增材制造工艺和新材料应用产生的非常规拓扑。在此设计步骤中使用的任何软件都应支持典型和非典型拓扑的设计探索。第三,探索实现下一代电驱动目标性能的主要途径之一是与材料工程相关的创新。一个好的电机设计软件应该包含广泛的材料库,包括电磁、热和机械特性的综合数据库。软件中的求解器技术应该能够用于根据制造商提供的材料和损耗数据准确计算迟滞和涡流损耗。它还必须能够支持分析由于温度变化、机械应力等引起的物理效应而导致的材料性能变化。第四,驱动由逆变器驱动,逆变器会对电机性能和系统效率产生重大影响。设计工程师通常需要能够考虑逆变器27、及其控制策略影响的分析功能。这包括评估开关损耗以及驱动谐波对电机性能及其NVH特性的影响。在设计的这个阶段,进行详细的多物理场冷却系统设计或NVH分析并不重要。但是,重要的是要确保欧姆和其他损耗不会降低电机性能,或者更糟的是,导致灾难性故障。因此,能够计算一些参数非常重要,这些参数将有助于确保电机安全在正常运行下不会受到损害。理想情况下,可以使用基于集总参数或低维耦合电磁-热耦合仿真来确保电机的热可靠性。同样,在此阶段不需要详细的NVH分析。然而,评估组件界面之间的力分布、表面节点力分布、气隙通量密度谐波含量和局部应力水平的能力非常重要。在Simcenter工具组合中提供了SimcenterS28、PEED和SimcenterMotorsolve工具,形成了一个出色的组合,可提供基于磁路的快速(秒)和基于有限元的高精度(秒/分钟)电机性能结果。SimcenterSPEED软件(1980年代后期发布)将分析磁路和基于模板的方法商业化,SimcenterMotorsolve软件(2008年发布)为基于模板的电机有限元分析工具。电机选型及设计迭代 13西门子数字化工业软件白皮书 Simcenter电驱动系统性能开发图9SimcenterSPEED(上图)和SimcenterMotorsolve(下图)示例这些工具的一些基本功能是提供各种保真度级别的多个分析选项。其中包括电流和电压驱动仿真、基于29、等效电路的PWM分析、D轴和Q轴分析、完整的基于有限元的瞬态和运动仿真等。SimcenterMotorsolve包括一个全面的磁性材料库,涵盖广泛的软磁和硬磁材料,冷却材料等。同时软件还包含一些其他扩展功能:包括永磁体退磁预测、系统模型接口和电磁力计算、输出节点力的能力、温度分布的计算以及使用电磁-热耦合仿真识别热点。模型还可以导入到SimcenterSTAR-CCM+软件中以进行基于CFD的电磁热耦合仿真。还可以使用与SimcenterAmesim的无缝连接以进行系统级分析,并连接到HEEDS软件,在设计阶段进行多目标设计优化、设计探索和灵敏度分析。在单个软件系列中实现如此全面的功能是独一无30、二的。Simcenter旨在为解决前面提到的问题和挑战提供解决方案。图9显示了SimcenterSPEED和SimcenterMotorsolve永磁同步电机模型的示例。以8极48槽永磁同步Leaf电机为例,给出了电机速度-扭矩-效率图,并使用SimcenterMotorsolve计算表面节点力分布。14西门子数字化工业软件白皮书 Simcenter电驱动系统性能开发上一步的主要目标是获得满足系统级选型期间确定的性能标准的单个或多个设计选项。另一个重要目标是确保为这些选择实施实用、经济高效。将其缩小到几个候选者后,接下来进行详细分析。在此阶段,可能会进行基于二维和/或三维有限元分析的电磁仿真,31、以验证电机性能,改进几何形状以优化磁通分布并减少泄漏,分析系统故障,包括退磁预测,灵敏度分析,耦合电磁热仿真,结构分析和设计优化。还评估了电机在各种负载条件(连续、峰值、启动和最大速度)下的性能。应该指出的是,其中一些分析实际上也可以在上一步中进行,尽管是低保真水平。计算密集型的(3D有限元和多物理场)通常留给这个阶段。需要注意的重要一点是,此阶段使用的分析方法应该是计算上可行的最准确的。对于大多数问题,这意味着将使用基于有限元的方法。从软件的角度来看,与上一阶段类似,关于所需功能可以说很多。但是,我们将重点关注与前面确定的工程和仿真挑战直接相关的方面,从与高效电机开发相关的挑战开始。准确计算32、电驱动效率有两个主要要求:第一,获得准确的场求解器,第二,计算损耗。事实上,这些要求是相互关联的。电机中有两种主要的电磁损耗源:欧姆(直流和交流)和铁损(包括迟滞和涡流损耗)。直流欧姆损耗是众所周知的,可以使用分析方法准确计算。交流欧姆损耗需要基于时谐场或基于瞬态场的有限元仿真。计算铁损困难的原因很复杂,包括模拟各种环境条件下的复杂材料行为、制造效应、电机控制策略的效果等。另一个重大挑战与多物理场仿真有关。在设计阶段,一旦电磁性能得到验证,就需要完全耦合的电磁-热仿真,以确保在峰值和额定条件下,电机的性能水平可以通过适当的冷却系统保持。需要温度升高对材料的电性能和磁性的影响。理想情况下,需要基33、于有限元的电磁-热仿真,其中传热系数基于经验分析和/或基于CFD的计算。在某些情况下,将基于有限元的2D电磁与基于3DCFD的热分析相结合也将是一个不错的选择。最终,电磁模型所需的保真度级别取决于要解决的特定问题。现在让我们考虑一下Simcenter处理这些问题的解决方案。Simcenter包含电磁、热(包括经验和基于CFD的求解器)仿真工具,例如SimcenterMAGNET软件是通用2D/3D电磁分析工具。它是第一个应用基于有限元的算法来求解麦克斯韦方程组的商业软件。自成立以来,它在开发电磁设备设计问题的尖端仿真功能方面一直处于领先地位。最近,西门子为SimcenterMAGNET增加了一34、个磁滞场求解器,它是提供精确场解决方案的行业领导者。考虑到前面讨论的设计挑战,我们需要在设计周期中考虑高阶效应。SimcenterMAGNET中的磁滞求解器是实现此目标所需的技术类型的一个例子。与传统方法相比,该技术显著提高了铁损计算的准确性。电机电磁性能仿真验证及优化 15西门子数字化工业软件白皮书 Simcenter电驱动系统性能开发设计容错和鲁棒设计是另外两个电机设计挑战。电机故障的一些典型来源包括线圈和绕组短路、导致轴偏心的轴承退化、电压波动引起的电流浪涌、过流或温度浪涌引起的永磁体退磁和/或其他物理损坏。此外,制造和处理效果和公差也属于容错和稳健设计的标准。另外,对轴承退化导致偏心率35、的影响进行建模需要耦合的六自由度机电仿真,这既耗时又困难。对于软铁材料,磁性(B-H)特性和铁损耗可能与制造商提供的数据有很大差异。对这些效应(包括材料非线性)进行建模可能需要高保真模型。针对这些,我们可以使用 Simcenter 中的一些工具进行分析。由于电气和/或热系统故障引起的故障条件可以使用 Simcenter MAGNET 进行模拟,包括使用耦合的电磁-热分析功能。由于轴承退化引起的机械故障可以使用SimcenterMAGNET六自由度运动建模功能进行分析。为了防止高压组件之间的短路,可以使用SimcenterMAGNET电场求解器计算电场强度。Simcenter MAGNET 3D36、 退磁仿真功能可用于识别永磁体中由于过流和/或高温故障而容易退磁的局部区域。通常,SimcenterMAGNET可用于确保大多数电气故障的容错能力。为了对源自制造和其他来源的统计不确定性进行建模,HEEDS可以与上面讨论的任SimcenterMAGNET模型一起使用。HEEDS还可用于进行灵敏度分析,多目标优化问题中的降维,相关空间研究等。图10显示了10极12槽永磁电机的三维SimcenterMAGNET模型,包括其退磁场预测。仿真结果可用于识别易受剩磁场弱化影响的区域,从而影响电机性能。这些类型的结果有助于保护电机性能免受系统故障的影响。图10轴向永磁电机(左)及其高温下的退磁预测场此外,37、在面对轮毂电机或者轮边电机的设计时,电机的轻量化设计问题也是十分重要的方面。为了提升整车车辆动力学特性,轮边或者轮毂电机的设计要在满足动力学要求下尽可能减小重量。面对这样的挑战,可以采用优化软件驱动电磁场仿真在满足性能前提下探索更多的轻量化的设计方案。图11显示了采用HEEDS驱动进行电机电磁场轻量化设计的流程。16西门子数字化工业软件白皮书 Simcenter电驱动系统性能开发图11基于HEEDS的电机定转子轻量化优化设计 17西门子数字化工业软件白皮书 Simcenter电驱动系统性能开发电驱动系统设计另一个重大挑战与多物理场仿真有关。其中结构强度、可靠性及振动噪声是结构方面主要关注的方面38、。对电驱动进行机械分析和NVH分析,以防止结构故障,以减少谐波的影响,避免共振并符合健康和安全标准。这一阶段的分析是在详细设计阶段,基于三维几何模型完成的。Simcenter3D提供完整的有限元前后处理环境,包括几何建模、清理、网格划分、网格质量检查、网格编辑、材料与单元属性定义、载荷与边界条件定义、分析工况定义以及各类后处理功能。这可以支持用户方便的进行结构强度分析。电驱结构多物理场仿真分析图12Simcenter3D电驱系统三维结构多物理场仿真对于电驱动系统的NVH仿真是典型的多物理场仿真的应用。下面我们以其为例详细说明。电驱振动噪声来源于电机电磁激励及减速器的齿轴激励。这些都会通过壳体振39、动辐射到空间中产生噪声。因此,系统的采样多领域及多物理场仿真分析获取准确的载荷以及进行恰当的振动噪声仿真分析是十分重要的。电磁仿真需要采用考虑运动的时域求解器,因此往往采用2D模型提高仿真分析效率。结构有限元模型往往为三维网格,求解采用频域算法。电磁仿真的模型和结构仿真模型是两套不同的模型网格。Simcenter3D中电磁力处理工具可以快速方便的解决从电磁仿真到振动噪声仿真之间电磁力处理的问题。对于电驱动NVH分析的载荷多体动力学分析工程师来说,高效便捷的建模工具非常重要。Simcenter3DMotion提供专门的参数化变速箱建模工具箱TransmissionBuilder。如下图13所示,40、基于该工具,用户可以根据变速箱的原理简图、各部件参数快速准确的得到变速箱的多体动力学模型。对于变速箱而言,合理的轮齿微观修形可以显著提高其性能。在TB中提供了完备的轮齿微观修形功能。18西门子数字化工业软件白皮书 Simcenter电驱动系统性能开发图13TransmissionBuilder工具箱基于Simcenter3DMotion中原有的的齿轮接触算法,TransmissionBuilder扩展增加了齿轮啮合力计算方法。在齿轮接触检测方面,增加了分片检测的功能,从而可以考虑齿轮修形、齿轮不对中引起的动态效应。对于齿轮啮合力/啮合刚度计算,软件提供了基于ISO标准及用户定义传递误差;基于解41、析公式计算以及基于柔性接触的高级算法三种方法。高级齿轮啮合力计算方法用于模拟轮辐结构刚度变化引起的齿轮啮合力动态效应。同时结合有限元分析,可以对轮辐结构刚度变化引起的齿轮啮合力动态效应进行精确的模拟。Simcenter3DMotion求解器基于时域进行求解,可以对系统进行柔性化建模处理,包括壳体的柔性化、轴的柔性化及齿轮的柔性化。电驱动总成的时域多体动力学模型载荷输入可以由电磁场仿真得到的转矩波动作为输入进行分析。在实际加载中可以考虑电机的外特性曲线。无论是结构激励还是电磁激励,都会激励起结构壳体的振动,进而产生噪声。因此,采用正确的方法和手段对壳体,尤其是对整个系统级的装配体进行动力学建模,42、获取准确的结构模型用于振动仿真分析是十分重要的。对于复杂结构来说最有效的方法是采用有限元模型修正的方法,通过试验验证仿真模型。通过试验振型与仿真振型的相关系数MAC、试验传函与仿真传函的相关系数FRAC、对仿真模型的置信度进行评估。通过Simcenter3D模型修正,进一步通过驱动有限元求解器的优化功能,可以完成优化迭代过程,从而使仿真模型与试验模型更加一致。19西门子数字化工业软件白皮书 Simcenter电驱动系统性能开发图14结构模态试验仿真相关性分析及模型修正在电磁激励和齿轴激励的共同激励下,Simcenter3D可进行电驱动总成振动噪声分析。软件支持模态法求解器和直接法求解器的结构求43、解。对于刚度随频率变化不大的系统和结构,可以采用模态法进行结构振动噪声响应分析,对于结构刚度随频率变化的部分,如考虑减震系统的影响时,则需要采用直接法进行振动噪声分析。Simcenter3D中提供的完整丰富的求解功能支持各种情况的求解。基于声波波动方程精确理论和声学有限元/边界元数值方法的工业标准级求解器,可以实现快速、准确的声学求解预测,并同时将最复杂的因素考虑进来,使用得到企业验证的声学有限元/边界元分析技术可以在保证求解速度、精度的前提下确保仿真分析的可信度。考虑到电驱动总成辐射噪声宽频段与高频的噪声特点,Simcenter3D中提供的多种快速求解技术帮助提高噪声分析效率。FEM-PML44、/AML完美匹配层有限元技术在将有限元求解速度提高10+倍的同时,极大地拓展声学建模的灵活性和仿真应用范围,该技术有些类似于无限元方法中的无反射边界层概念,但理论上比无限元先进,可以认为是无限元的替代技术,可以大大减少声学网格的数量提高多频率点分析求解效率。FEMAO自适应阶次声学有限元求解器打破了原有六分之一波长的网格尺寸划分要求,可以从一个较粗的有限元网格进行求解,并且随着分析频率的增大有自动的进行加密。这样就使得每个分析频率都可以采用一个较少的自由度进行求解。从而使得该求解的速度相对于传统有限元得到了很大幅度的提升,并且需要很少的内存。因此对于电驱求解需要涵盖几百Hz到上万Hz的问题,采45、用自适应求解技术可以大大提高分析效率。Simcenter3D利用了ATV传递函数技术,该传递函数建立起辐射表面的结构振动与输出场点处声压级之间的联系。ATV和载荷无关,这意味着ATV技术特别适合于多工况分析,像电驱动总成加减速工况和结构设计参数优化。该技术在载荷和设计参数变化的仿真计算中显示出巨大的优越性,因为只要不改变有限元模型的拓扑结构就不需要重新运行求解器。另一个优点是与结构计算相比,ATV计算频带更宽,因为ATV是频率的光滑函数。依据电驱动总成的几何结构,建议使用5Hz到25Hz宽的频带。使用大的频带可以节省声学响应的计算时间。20西门子数字化工业软件白皮书 Simcenter电驱动系46、统性能开发图15ATV快速求解技术在结构设计中另一个方向是采用先进的仿真计算实现结构轻量化设计。Simcenter3D创成式优化设计可以有效帮助用户实现这一需求。这是一个人机交互、软件自我创新的过程。根据输入者的设计意图,根据“良性”的问题结构以及外部约束,通过“创成式”系统,生成潜在的可行性设计方案几何模型,然后进行自动化设计综合,从而筛选出设计方案推送给设计者进行最后的决策。创成式优化设计方法包括拓扑优化、形状优化、制造优化甚至是规则驱动的参数技术。这些优化设计(有时称为仿生化)不能通过传统的设计方法完成,也不能使用传统的减法制造方法生产。与传统设计方法相比,创成式设计让产品开发人员有机会47、探索更多设计方案。Simcenter3D创成式优化设计软件,覆盖产品概念设计、详细设计及验证等各个环节,包括模型设计、拓扑优化、模型轻量化设计、模型验证、模型打印准备、模型质量检查等环节,所有业务环节都可以在统一的软件环境实现,不需要切换软件,不需要数据格式转化,这是西门子独有的技术优势,帮助用户对现有业务进行流程化,提高业务开展的效率。图16创成式结构轻量化优化设计 21西门子数字化工业软件白皮书 Simcenter电驱动系统性能开发电机在工作状态下产生的损耗,都会以热量的方式表现出来。混合动力汽车或者纯电新能源汽车的驱动电机采用的是永磁同步电机,永磁同步电机对散热的要求极高,这是因为磁铁在48、高温的环境下是可以消磁的,若因电机散热不佳导致消磁车辆失去动力,这将会造成车辆运行的危险性。新能源汽车电驱动系统由于其结构小、能量密度高的特点,会造成热量更加集中,从而需要更加有效的散热设计。而且,由于驱动电机和变速器集成化设计的需要,电驱和变速器的热量都需要更小、更简单的冷却方式,以有效满足散热设计。电驱散热性能分析的目的在于获得电驱动系统在不同工况下的三维详细温度场,判断冷却系统的设计是否满足电驱散热的需要,如果不满足设计需要,则需要修改冷却系统设计,预测冷却系统性能以满足散热的需要。新能源汽车电驱动系统散热主要有3种方式:风冷、水冷、油冷,或者多种冷却方式混合使用。风冷是通过冷却风扇直接49、吹拂电机的方式进行冷却。这种冷却方式的散热不均匀,散热效率低,散热效果不好,风机运行的噪音相对较大。这种冷却方式适合于电机输出功率不高的微型车。水冷则是用冷却液充满电机壳体内部的水道,然后连接一个外部的散热量,从而把电机的热量带走。这样做的好处是电机和电池包可以共用一套冷却系统。但是水冷方式的缺点也很明显,由于电机的高温部分主要集中在定子绕组的端部,热量要通过绝缘层、定子外壳和水道才能被冷却液带走,这无疑会影响散热的效果。而且由于额外的水道,电机的体积也会增加。油冷的方式是把润滑油直接喷淋在定子绕组的端部,直接对高温部件进行冷却,同时通过转子旋转轴开孔的方式,将冷却液喷淋到转子上。研究表明,在50、相同工况下,油冷电机的内部各温度比水冷电机的内部温度要低15%以上,油冷电机达到热平衡的时间会更短。因为电机在运转的过程中,绕组的端部往往是发热最严重的区域,差不多能占到电机热量的40%。而更深层的转子深处的热量也无法带走,这就衍生出全新一代油冷散热技术,直瀑油冷,不仅在绕组端部油液沁入散热,更是在转子整体做油液喷淋,使得整个电机的散热效能达到最佳。油冷方式可以把电驱和变速箱集成在一起,减小了设备尺寸,这是当前新能源汽车电驱散热研究的重点方式。但油冷电机散热性能的分析存在着一些应用的困难,这是因为:由于电驱动系统的转子较高的转速(一般高达每分钟数万转),而且喷淋冷却是典型的多相流(空气相,润滑51、油相)应用,因此流体侧的仿真需要使用瞬态模拟的方案,而且其时间步长较小,需要更多的时间步才能达到“稳定”。而电驱仿真所关心的“稳定”固体温度场,由于固体热容性的存在,需要更长的物理时间(通常数分钟)才能达到。电驱散热性能分析 22西门子数字化工业软件白皮书 Simcenter电驱动系统性能开发因此,如何解决这两个相互矛盾的点,是油冷电机散热性能分析的重点和难点。传统上基于有限体积方法进行仿真分析,其计算时间通常需要数周,这在工程上是不经济的,也是不允许的。西门子Simcenter采用将流动和换热分离开来,分别建立各自的模型,流体采用瞬态模拟,固体采用稳态模拟,将两个模型耦合的方案进行油冷电机散52、热性能分析。在该方案种,使用SimcenterSPH-flow进行喷油的模拟,而固体温度场使用SimcenterSTAR-CCM+进行建模。SimcenterSPH-flow是一款无网格、基于光滑粒子流算法的计算流体力学(CFD)软件,使用SimcenterSPH-flow可以无惧复杂几何、运动即可完成流体仿真,因为基于粒子的方法,不需要划分网格,同时其多相计算效率相对于传统的CFD方法提高了6倍。SimcenterSTAR-CCM+是一款优秀的、基于有限体积法的CFD软件,其在复杂几何处理、计算效率上相对于同类型软件具有明显优势。在耦合方案中,SimcenterSPHFlow计算瞬态液体喷淋53、以及对流换热,将对流换热系数传递给SimcenterSTAR-CCM+;SimcenterSTAR-CCM+进行问题固体温度场计算,将固体表面温度传递给SimcenterSPHFlow。通过多次反复的耦合过程,直至达到温度场“稳定”状态。下图说明了耦合的过程。图17Simcenter电机散热模拟耦合流程使用Simcenter耦合方案,电驱动系统油冷散热分析周期从数周降低为数天,计算效率提高了6倍,可以有效满足产品开发周期的需要。23西门子数字化工业软件白皮书 Simcenter电驱动系统性能开发此外,电驱散热性能分析中,可以使用HEEDS进行优化分析,通过HEEDS,可以优化冷却系统设计,比如54、喷淋孔位置和流量,从而优化产品设计,提高散热设计的性能。24西门子数字化工业软件白皮书 Simcenter电驱动系统性能开发对于新能源汽车来说,电控系统相当于整车的“大脑”,它的性能决定了车辆能耗、排放、动力、舒适性等主要的性能指标。在节能减排的要求下,电控系统的整体呈现功能越来越复杂、集成度越来越高的发展趋势,这意味着电控系统的散热问题愈发凸显。事实上,50%以上的电子系统失效都是由于温度导致,所以必须采取高效的冷却方式以及合理的散热设计,才能保证电控系统的安全运行。电驱电控系统散热设计中最核心的部件是电驱主控制器和功率变换器(包括DC/DC变换器和DC/AC逆变器),冷却方式可以采用风冷或55、者液冷。在新能源汽车的集成化电驱动系统中,主要以液冷设计为主,与电机、电池冷却方式一致,结构更为紧凑,便于系统化设计和管理。对于功率稍小的辅助控制器,也会根据安装空间等条件,选择被动冷却或风冷的散热方式。电控系统散热设计的首要目的是获得关键功率器件结温和控制器整体的三维温度场,确认电子元件处于安全的工作温度范围。除此之外,液冷分析还需要根据分配的冷却流量,通过设计和优化冷板结构,保证功率器件温度的均匀性,同时尽量降低冷板压降,减小流动损耗。被动冷却或风冷需要优化散热器结构,进行风扇选型和位置优化,避免散热路径上出现导热瓶颈或热风回流。电控散热设计主要有三个难点:1,跨学科跨部门协作。电控系统的56、散热设计与电子电气设计和结构设计密不可分,热设计工程师应用来自电子电气工程师的EDA文件和来自结构设计工程师的三维CAD模型进行热流仿真分析,在设计发生变更时需要及时同步模型数据。不同部门的工程师所用工具能否无缝集成,模型数据是否有统一真实的来源,决定了热设计的效率。2.难以在设计早期定位潜在散热问题。很多散热问题在概念设计阶段就已经存在了,只是传统的设计方式通常先分别进行电子电气和结构设计,之后再进行热符合性验证,散热问题发现得比较晚,导致大量的返工和重新设计。3.汽车电控系统仿真前处理工作量大,影响研发周期。对于集成度高的电驱电控系统如三合一系统,整体结构非常复杂,如果在传统CFD工具中进57、行整机热流分析,几何清理及网格划分可能花费数天甚至数周的时间,影响整体开发进度。故而很多时候,不得不将三合一系统拆分,分别进行分析设计。但电控模块所处环境复杂,各部分的流场和温度场互相影响,分开分析很难给定准确的边界条件,影响分析准确性。如何解决上述难题,是提高研发效率、加快设计创新的重点。SimcenterFlotherm(XT)和FloEFD是西门子Simcenter解决方案中专为电子热设计而开发的仿真工具,旨在帮助研发团队应对电控系统热设计中的挑战。电控系统散热分析 25西门子数字化工业软件白皮书 Simcenter电驱动系统性能开发SimcenterFlotherm(XT)内置Smar58、tpart参数化建模模板和大量供应商数据库,还拥有FlothermPACK及PackageCreator封装建模库,提供机箱、PCB、风扇、散热器、热管、热界面材料等模型和数据,以及功率电子和控制器芯片的常用封装模型如BGA、QFN、TO等等,可直接在概念设计阶段快速建立主控制器和功率电子器件的简化模型,从而在没有详细结构和电子电气设计的时候,提前发现潜在的散热问题,论证散热方案,优化PCB布局,为结构和电气工程师提供设计建议。SimcenterFLOEFD是业界领先的CAD嵌入式多功能CFD仿真工具,能够集成在所有主流CAD设计软件中,无需切换工具,即可在结构设计工作环境中完成全部的CFD前59、后处理和求解。当设计发生改变时,CFD仿真设置也同步更新。FloEFD独特的SmartCells网格技术能够自动识别流体域,使得工程师无需对复杂几何模型做手动简化和清理,同时自动进行网格加密和边界层处理,能够节省70%-80%的前处理时间,从而大幅提高散热设计效率。通过FloEFD自带的设计优化模块,或集成到HEEDS平台,可以自动优化冷板、散热器结构,广泛应用于功率电子模块或电控系统整体的液冷散热设计。图18SimcenterFlotherm中的ECU建模及热仿真图19SimcenterFloEFDIGBT冷板热分析(左)及PEU热设计(右)SimcenterFlotherm(XT)和Flo60、EFD都具有全面兼容的EDA数据接口,可以自动将二维EDA设计转化成三维热仿真模型,从而将电子电气设计与散热设计无缝集成。26西门子数字化工业软件白皮书 Simcenter电驱动系统性能开发考虑到车载电子所处的高温和振动环境,工程师也可以从FloEFD中输出多种格式的三维温度场和流场结果,结合有限元工具进行热-结构耦合分析,如封装焊球的蠕变和热疲劳分析。Flotherm(XT)和FloEFD还可以输出边界无关的降阶模型,与一维系统仿真工具结合进行1D-3D协同分析,使系统设计具备预测温度的功能,例如在液冷系统设计中考虑流量分配对IC结温的实时影响,分析逆变器中IGBT温度在真实驾驶循环中的瞬态61、变化,以及动态温度调控策略仿真等等。27西门子数字化工业软件白皮书 Simcenter电驱动系统性能开发对于电驱系统的仿真分析,传统方法是将不同的结构分割,然后再分领域的进行设计仿真分析。不同的仿真分析之间相互独立,系统级集成往往在后期阶段完成。或者采用多物理场联合仿真的方法,创建二维或者三维模型,采用有限元方法进行仿真分析,这些模型相对精度较高,但是其求解过程往往需要消耗大量的时间和计算资源。电驱动系统性能集成化分析图20传统集成分析流程:顺序仿真(上图)和三维多物理场仿真(下图)图21集成化的系统仿真随着开发周期压缩的压力和产品集成度的提高,采用集成化的方式进行系统级的设计仿真,同时兼顾电62、机和控制器的性能的方式应运而生。即在系统级采用一维模型,设计空间或者实时仿真。在部件级采用一维、二维和三维模型的混合模型。28西门子数字化工业软件白皮书 Simcenter电驱动系统性能开发在其中,一维系统仿真往往都会采用SimcenterAmesim来搭建,不同层级的零部件模型会通过联合仿真或者模型降阶的方法与系统模型联合,最终形成一个包含各个层级维度的系统模型。Simcenter中的工具及其直接和间接连接提供了一个独特的平台,可用于探索传统设计方法的替代方案。同时Simcenter将整个过程做的更加自动化、接口更加方便,以同时方便设计工程师和仿真工程师来使用。下面我们将举几个典型的案例予以63、说明。动力性能迭代验证获得电机的详细设计参数后,工程师利用SimcenterAmesim将这些参数导入整车及电驱动系统的详细模型中,完成对电机详细设计的整车级迭代验证。验证内容包括初始设计阶段所述动力性和经济性的各项指标。该阶段所用到的电驱动系统模型较初始阶段的功能模型颗粒度更为精细,具体表现为电驱动系统模型对控制器和电机本体进行区分,电机本体外特性不再采用用户定义的方式,而是根据电机设计部门给出的详细参数计算得到。同样的,控制器功率单元的效率也能够根据器件手册中的半导体工作特性计算得到。综上所述,电驱动系统的详细动力性能在这一阶段得到了验证。散热性能分析及热管理策略电机内部温升过高不仅会缩短64、电机内部绝缘材料的寿命,而且会降低电机的运行效率,使得发热量增加,造成电机温度进一步上升,形成恶性循环,严重影响电机寿命和运行安全性。据统计,30%40%的永磁电机失效是由电机温升过高引起的。因此,采用高效的散热系统抑制电机温升是电机向高效率、高稳定性和高可靠性方向发展的关键。相较于风冷散热,液冷散热具有更高的换热效率,可以达到前者的50倍,适用于电机发热量大,热流密度高的散热场合。因此,车用电机的多采用水冷或油冷这两种液冷散热方式。水冷散热系统的流道结构是影响其冷却效率的关键因素,工程师通过优化图22加载电机详细电磁性能的整车级指标验证 29西门子数字化工业软件白皮书 Simcenter电驱65、动系统性能开发流道结构参数提高水冷散热的冷却效率。通过通过增加流道数量、在冷却流道中添加扰流结构和增加冷却水流量等方式可以有效提高冷却效率,但同时也导致压力损失明显增大。因此,在实际应用中需要综合考虑水道换热能力和压力损失以设计合适的水道结构。直接油冷散热系统的冷却油与电机内部发热部件直接接触,具有极高的散热效率,是解决高功率密度电机散热难题的有效方案,目前正在被越来越多的电驱动系统供应商所采纳。但直接油冷循环系统的设计复杂度比水冷循环的设计更加复杂,需要较为详细的仿真验证与评估过程才能使系统散热效率达到最佳。无论是水冷散热还是油冷散热系统,都涉及到液冷循环回路的流量和压力计算,以及冷却工质和66、电机本体间的换热计算。通常采用的方法是通过CFD和热网络法相结合的方式,利用CFD精细化的网格划分计算得到电机液冷循环系统在典型工况下的稳定流动状态以及换热效果,然后通过离散化处理,在多学科系统仿真环境中得到电机本体、减速器、以及液冷循环系统的热网络模型,进而加载动态工况完成进一步的散热设计验证。采用SimcenterAmesim可以帮助工程师快速地从电机设计工具如SimcenterSPEED、MotorCAD导入当前设计所对应地电机本体热网络模型,同时,用户可以在SimcenterAmesim环境下对该热网络模型进行任意调整已完成电机本体、减速器、液冷循环系统的集成,从而在保持仿真精度的同时67、,大大提升仿真闭环动态工况下的仿真计算速度。图23电机热网络法的仿真评估的自动化实现流程 30西门子数字化工业软件白皮书 Simcenter电驱动系统性能开发控制器功率模块散热设计控制器功率模块为电机控制器的核心部件,电机驱动系统的大容量控制需求,使功率模块向高频化、大功率化以及高度集成化方向发展。IGBT/SiC是目前车用电机控制器功率模块普遍采用的半导体技术,同时也是电机控制器的主要热源,在处理波动的功率流工作过程中,IGBT/SiC产生的功率损耗导致其结温的升高与波动,导致芯片性能衰减,甚至造成键合线断裂等失效形式。因此,进行结温估算研究对于提高电驱动系统可靠性,实现精准热控制及部件保护68、具有重要意义。目前常用的结温估算模型例如Foster热网络法,需要通过热阻测试仪,例如:T3STER,或基于CFD的专业电子散热仿真工具,例如:SimcenterFloTherm,测量或计算得到功率模块的降阶热网络模型。该热网络模型可以直接导入SimcenterAmesim中与电驱动系统其他部件模型集成,并应用于动态闭环工况的仿真。工程师采用上述方法能够大大缩减仿真计算耗时,从而加快功率模块散热的设计研发速度。图24液冷循环系统的流量分配仿真评估图25功率驱动模块的降阶热模型与SimcenterAmesim中整车及液冷系统集成 31西门子数字化工业软件白皮书 Simcenter电驱动系统性能开69、发NVH性能集成验证车用永磁同步电动机具有结构紧凑、功率密度高、气隙磁通高以及转矩惯性比高等优点,电机输出转矩平滑度是衡量驱动系统性能的重要指标,而电机电流中的高次谐波是影响电机输出转矩平滑度的主要因素。造成电机电流谐波因素主要有两方面原因:1)电机本体方面,如齿槽效应、绕组分布形式、磁路磁饱和效应、转子磁极结构等引起的电机气隙磁场畸变;2)逆变器方面,如开关器件的死区时间、管压降等非线性特性。同时,减速器齿轮的刚度和惯量也会引起电驱动系统输出轴上的扭矩波动。因此,在设计电驱动系统的时需要对各因素引起的输出扭矩波动进行综合考虑和优化。采用SimcenterAmesim多物理系统仿真平台搭建的电70、驱动系统及整车驾驶性模型,可以精确复现电驱动系统各部件引起的扭矩波动。首先工程师将电机电磁仿真所获得磁链及铁损参数Map文件导入SimcenterAmesim,该参数文件用于精确计算电机转子在不同角度与电流幅值相位下的电磁扭矩。同时SimcenterAmesim中搭建的详细的驱动电路模型可以体现由PWM脉宽调制所产生相电流高阶谐波。工程师通过仿真可以对电驱动系统输出扭矩波动的各阶分量进行跟踪分析,同时开发用于抑制波动的软件控制策略,如谐波注入功能。图26系统仿真中的NVH性能评估与优化 32西门子数字化工业软件白皮书 Simcenter电驱动系统性能开发控制算法验证与虚拟标定(MIL)Simc71、enterAmesim提供了各种类型电机的本体模型及其常规控制算法,包括:直流有刷、直流无刷、永磁同步(凸极式/隐极式、三相/六相/九相)、感应电机、开关磁阻电机。该平台提供的整体解决方案适用于各类电传动部件的建模与仿真。例如:动力总成中的主驱电机、启动发电一体机,底盘中的转向助力电机、线控制动电机,热管理系统中的空调压缩机、循环泵驱动电机,车身中的座椅调节电机、车窗升降电机等。以车用主驱电机中常见的高速永磁同步电机及其FOC控制、SVPWM调制技术为例,如下图所示。工程师利用该模型可以快速地完成控制算法功能性验证,控制电流的幅值/相位标定,电流环跟踪控制的PID参数整定,评估不同PWM调制技72、术、载波频率、死区宽度对电流谐波成分的影响。电控系统策略开发与在环验证图27电机控制算法验证FOC+SVPWM图28电机虚拟标定及整车能耗评估工作流程 33西门子数字化工业软件白皮书 Simcenter电驱动系统性能开发电机控制器软件在环测试(SIL)上节内容实现了电驱系统控制算法开发过程中模型层面的验证,为了保证软件实现后的功能与算法模型保持一致,特别是在MCU硬件具备部署条件之前,或者已经具备部署条件但由于软件成熟度不足而可能造成调试过程中硬件损坏,可以通过软件在环测试对控制程序代码进行功能验证。这部分工作主要分可为两类:第一类只关注实现控制算法的应用层软件测试,目标编译平台无需与控制器保73、持一致,该方法的优点是流程简单、测试迭代周期短;第二类测试方法需要将应用层软件(SWC)与符合AutoSAR架构的基础软件(BSW)进行集成,通过虚拟ECU完全模拟SWC与BSW在目标处理器上的运行环境,相较于前者该方式的优势在于控制软件的测试范围更加全面,更加符合软件真实运行场景。针对第一类即仅应用层软件的在环测试,SimcenterAmesim中的电驱系统被控对象模型可与应用层算法软件的C代码通过联合仿真进行闭环测试,用户程序代码可运行在VisualStudio等常用集成开发环境中。针对第二类与AutoSAR基础软件集成后的测试,SIEMENS旗下Capital产品线可提供全面的测试解决方74、案:从用户MCU控制算法的AutoSARSWC封装、网络通信,到AutoSAR架构模块配置、与基础软件进行集成,最后部署在虚拟ECU环境中运行。详情可咨询如下链接:https:/ 34西门子数字化工业软件白皮书 Simcenter电驱动系统性能开发电机控制器硬件在环测试(HIL)电驱系统控制器原型开发完毕之后,还需要经过硬件在环测试(HIL)完成进一步的验证。此时包含控制功能的完整软件程序已经能够部署在目标处理器上,外设电路如:数模转换、信号调理、电气隔离、通信模块等已经过上电测试,功率主电路件也已经具备测试条件。这一阶段的根据用户的不同测试需求,可以采用信号级HIL、功率级HIL、机械级HI75、L(测功台架)完成。系统测试的真实度逐级上升,但同时测试成本和周期也在逐渐提高,测试范围逐渐减小。Simcenter电驱系统解决方案支持在上述各级HIL系统上部署运行,其中电机本体及逆变器的仿真模型可通过SimcenterMotorsolve和SystemVision生成VHDL硬件描述语言文件,综合布线生成网表后可下载到FPGA上配置实现;相对应地,控制算法、电驱系统系统热管理模型、电池模型、整车模型及驾驶工况等可通过SimcenterAmesim编译生成运行在实时仿真平台CPU上的可执行文件。图30电驱系统硬件在环仿真 35西门子数字化工业软件白皮书 Simcenter电驱动系统性能开发工76、程设计领域走向数字化,振动噪声及疲劳工程师也面临挑战,需要用更少的资源完成更多的任务,并在设计流程中尽早完成相关工作。SimcenterTestlab试验解决方案应运而生,旨在使试验更加方便和高效,它是试验部门赖以提高试验效率,保持数据质量,并实现更高投资回报率的解决方案。电驱系统性能开发过程中,试验测试手段至关重要,在每一个阶段都起到非常关键的作用。电驱系统振动噪声及疲劳试验验证SimcenterTestlab软件是基于试验工程的集成解决方案,将多通道数据采集与完整的测试、分析和报告流程相结合。SimcenterTestlab软件与SimcenterSCADAS数据采集硬件系统无缝集成。Si77、mcenterSCADAS系统以其优异的测试性能著称,可在试验室和现场提供测量质量和精度。SimcenterTestlab可以广泛地涵盖噪声振动工程师们所需要的所有试验功能,无缝集成了结构动力学试验、旋转机械试验、声学试验和传递路径分析等各种试验及分析工具。在疲劳试验领域,SimcenterTestlab具备最先进的专业技术手段,为道路载荷数据的采集和处理提供端到端的解决方案。结构动力学试验SimcenterTestlab结构动力学试验是一套全面的结构动力学和模态试验分析软件。表征结构的结构动力学特性在过去是一个漫长而复杂的过程,涉及耗时的参数设置以及大量的重复性试验。现在情况不再是这样了。将78、SimcenterTestlab结构动力学试验软件和SimcenterSCADAS数采系统相结合,可以轻松地执行大型结构的模态试验,整个试验周期只需要几个小时,而不再需要耗费好几天的时间。因此,您可以更专注于找出振动问题的根源,应用强大的分析工具来探索结构的薄弱环节。无论是小型结构的锤击测试,还是数百上千通道的大型结构模态试验,我们都拥有丰富的模态试验经验,可以帮助您提高试验效率。图31测试在NVH及疲劳耐久性能开发中的作用 36西门子数字化工业软件白皮书 Simcenter电驱动系统性能开发旋转机械试验SimcenterTestlab旋转机械试验为您提供一套完整的旋转机械振动噪声测试与分析解79、决方案,帮助您开发静音、高效、可靠的产品。SimcenterTestlab旋转机械试验的专用模块可帮助您应对发动机、压缩机、电机、泵或轴等系统中复杂的机械振动噪声问题。为了助力工程师的振动噪声故障诊断和产品性能优化工作,SimcenterTestlab旋转机械试验提供了全套的试验分析工具,包括瀑布图、阶次跟踪、时间数据采集、后处理分析以及其他各种专业分析功能,帮助您分析和查看大量的试验数据。图32电驱系统模态测试示例图33旋转机械试验结果分析示例基于部件的传递路径分析及虚拟样机装配技术传递路径分析(TransferPathAnalysis,简称TPA)技术,可以实现对各个激励源到目标点的贡献量80、进行定量的评估,其中基于部件的TPA技术(Component-basedTPA)是一项相比较新的技术。部件TPA将激励源的自身载荷(刚性约束力)特性与频域子结构理论相结合,可以实现目标点的响应预测和不同整机配置方案的对比分析。可以对大量变种型号产品的NVH性能,进行快速地预测和评估。37西门子数字化工业软件白皮书 Simcenter电驱动系统性能开发SimcenterTestlab虚拟样机装配基于TPA技术,能够帮助用户实现整机的虚拟装配,从而在产品研发的早期阶段,就能够对整机NVH性能进行预测,利用所有子系统和零部件数据(无论是来自试验还是仿真),完成对各种可能设计方案的快速评估。疲劳耐久试81、验SimcenterTestlab软件是一套集成式、端到端的疲劳耐久试验解决方案,包含完整的道路载荷数据采集及后处理分析功能。通过单一软件平台,您可以完全掌控所有工况的数据采集任务。将具有通用信号调理功能的多通道数据采集,与一整套通道设置、测试、验证、报告及数据共享工具相结合,与SimcenterSCADASRS或SCADASRecorder数据采集硬件无缝集成,将使您更有信心在更短的时间内、以更少的错误完成疲劳耐久试验工作。图34使用接触力和刚性约束力预测的目标响应和测试结果对比图35SimcenterTestlab虚拟样机装配技术预测整机NVH性能图36专为疲劳耐久性测试研发的数据采集设备82、SimcenterSCADASRS 38西门子数字化工业软件白皮书 Simcenter电驱动系统性能开发电驱动系统的市场趋势对测试过程有相当大的影响。需要有大量及灵活的电驱系统,以应对大规模定制的全球趋势。随着系列及型号复杂性的增加,物理原型的反复创建和测试成为解决问题的一种非常无效的方法。因此,开发过程变得越来越由仿真驱动。然而,这并不意味着测试工程师的工作量减少。恰恰相反,所有复杂性、创新性和个性化意味着更多的变体、更多的组件和系统、更多的创新设计探索以及对质量问题的更多关注。这需要测试、验证、确认和认证。为了成功开发匹配性最佳的电驱动总成,仿真和测试工程师密切合作至关重要。只有能够通过合83、并这些流程创造协同效应的制造商才能有效地在功能性能要求之间找到适当的平衡。这需要能够联合两个世界的测试工具。例如,其中包括用于验证、关联、处理和报告的仿真数据接口,以及基于实际测量和仿真模型创建虚拟通道的功能。在整个产品管理周期中,测试流程必须不断发展,以应对大量的测试工作和更快的模型驱动设计迭代。工具需要更具适应性来管理各种测试活动。测试过程需要更加透明,并集成到设计和开发中,数据需要在整个链条中一直链接,以匹配最终产品。根据最终产品验证和认证,实现这一关键可追溯性水平的方法是获取高质量测试数据,并将其与原始仿真模型进行关联或匹配。借助Simcenter产品组合,测试世界开始了这一旅程,将测84、试融入仿真领域。作为Simcenter产品组合的重要组成部分,面向下一代用户的新测试平台SimcenterTestlabNeo将提供一种多功能工具,可以开发数字孪生流程,同时支持设计流程中对高质量数据的需求。它为高效的测试过程提供了一个平台,一个可以通过仿真闭环的集成过程。SimcenterTestlabNeo通过使用称为SimcenterTestlab基于模型的系统测试(或MBST)的过程将模型正确放入流程中,从而实现仿真-测试闭环。该系统允许从SimcenterAmesim软件对多物理场仿真结果进行模型驱动的数据选择。使用测量的输入,它可以动态创建基于模型的虚拟通道。它在任何开发阶段都提供85、基于物理和虚拟组合测试的全系统验证。使用SimcenterTestlab测试通过仿真实现闭环,从而深入了解产品或系统的实际功能性能。SimcenterTestlabNeo提供对SimcenterAmesim数据的模型驱动访问,具有称为SketchViewer的功能。在SimcenterTestlabNeo桌面中,测试工程师可以访问来自SimcenterAmesim的仿真结果并浏览系统仿真模型。然后,他们可以以图形方式与模型交互,并选择模型的一个或多个组件。与所选组件对应的仿真变量会立即列在SimcenterTestlabNeo中,并可用于可视化、报告或SimcenterTestlabNeo的后86、处理。借助草图查看器,OEM工程团队可以减少关联仿真和测试结果所花费的时间。此外,它们消除了因使用不同的后处理平台而导致的错误和不确定性。电驱系统基于模型的系统测试 39西门子数字化工业软件白皮书 Simcenter电驱动系统性能开发图37基于模型的系统测试在电驱系统开发中的应用SimcenterTestlabNeo还引入了ProcessDesigner功能。这种完全可定制且灵活的功能可加快分析速度,支持多学科分析,并将仿真模型嵌入到任何流程中。流程设计器支持在创建的流程中集成功能模型单元。功能模型接口(FMI)是一种新的开放式接口标准,可方便地交换来自不同仿真环境的模型。SimcenterT87、estlabNeo支持FMI(修订版2)协同仿真标准。在此过程中,Simcenter测试实验室流程设计器可以充当协同仿真母版。仿真模型的输入和输出与活动过程中的所有现有分析方法耦合。所有模型变量都是针对测试期间的实际操作条件计算的,并且生成的时间轨迹以测试数据格式作为附加虚拟通道提供。Simcenter通过集成其仿真和测试工具,在任何开发阶段加速系统测试。新的基于模型的系统测试功能提高了整个系统开发周期中使用的工具和方法的一致性,并在整个开发周期中使用虚拟模型、虚拟物理组合模型和物理原型进行特定属性评估。40西门子数字化工业软件白皮书 Simcenter电驱动系统性能开发Simcenter是西88、门子数字化工业软件为研发数字孪生开发的全新平台,是一个灵活、开放和可扩展的仿真和测试解决方案组合,支持客户在数字化转型中的各类创新活动。该组合涵盖设计研发所需的系统仿真、机械仿真、流动与传热仿真、电磁仿真以及物理测试五大领域,以数字主线联通上述领域,打通数据壁垒。核心产品包括创成式架构设计评估SimcenterStudio,机电液热系统建模与仿真平台Amesim,电机设计和电磁场仿真软件SPEEDMotorsolve及MAGNET,集成结构,疲劳,电磁,振动噪声等多物理场的仿真平台Simcenter3D,专注于通用流体力学分析的STAR-CCM+SPHFlow,市场领先的电子散热仿真工具Flo89、Therm/FloEFD等。此外,Simcenter还专门提供物理测试硬件,以及多学科优化软件HEEDS,与上述软件产品一起构成完整的研发数字孪生体系。西门子还为客户提供工程服务,依靠深厚的行业专业知识和技术诀窍,为客户在数字化转型过程中保驾护航。Simcenter产品组合介绍Simcenter StudioSimcenterStudio是Simcenter投资组合中的一个应用程序,用于在早期概念阶段生成和评估系统架构。该软件包括专利技术,工程师和数据科学家可以创建新颖和拓扑不同的系统架构。SimcenterStudio还将系统仿真、控制方法和强化学习结合在最先进的机器学习和科学计算堆栈之上,90、以自动模拟和评估数百个这样的架构。这使得工程师和数据科学家可以在生成工程的计算笔记本中创建用户定义的过程。41西门子数字化工业软件白皮书 Simcenter电驱动系统性能开发Simcenter AmesimSimcenterAmesim是领先的集成、可扩展的系统仿真平台,允许系统仿真工程师虚拟评估和优化机电系统的性能。这将提高从早期开发阶段到最终性能验证和控制校准的整体系统工程生产力。SimcenterAmesim将现成的多物理库与面向应用程序和行业的解决方案相结合,这些解决方案由强大的平台功能支持,可以让您快速创建模型并准确地执行分析。这种开放环境可以很容易地与主要的计算机辅助工程(CAE)91、、计算机辅助设计(CAD)和控制软件包相结合。42西门子数字化工业软件白皮书 Simcenter电驱动系统性能开发Simcenter SPEED/MotorsolveSimcenterSPEED提供了大多数主要电机类的理论和物理模型(例如永磁体和电励磁同步,感应,开关磁阻,刷直流,绕线场换向器和轴向磁通)及其驱动器。SimcenterMotorsolve是一个完整的设计和分析解决方案,用于永磁,感应,同步,电子和电刷换向电机。该软件利用有限元分析与一个直观的界面,精确模拟电机。基于模板的接口易于使用,足够灵活,可以处理几乎任何电机拓扑,并提供自定义转子和定子。典型的有限元分析操作,如网格和求解92、器细化,绕组布局和后处理(包括一维模型的导出)由软件自动化完成。只需单击鼠标,就可以获得性能参数、波形和现场图。Simcenter MAGNETSimcenterMAGNET2D/3D是一款强大的电磁场模拟解决方案,可用于电机、发电机、传感器、变压器、执行器、螺杆管或任何带有永磁体或线圈的组件的性能预测。有了这个高效和准确的软件,您可以优化,设计和分析简单到复杂的电磁和机电设备。SimcenterMAGNET虚拟原型既节省成本又节省时间。参数化和优化研究允许探索多种配置以提高性能。通过对极端操作条件的精确复制,可以深入了解损耗和温度热点、永磁体退磁、未使用材料以及故障条件下的故障分析。43西门93、子数字化工业软件白皮书 Simcenter电驱动系统性能开发Simcenter 3DSimcenter3D是一个全面的、完全集成的CAE解决方案,这一解决方案包含了广泛的、精确高效的三维CAE解决方案,包括有限元分析、边界元分析、流体动力学与多体动力学等数学方法,涵盖结构分析、结构动力学、疲劳仿真、增材制造、电磁仿真、多尺度材料和复材分析、热流多物理场仿真、碰撞安全、多体动力学、声学仿真等十大应用方向,适用于复杂的、多学科的产品性能工程。该软件在模拟效率方面提供了革命性的改进。凭借先进的3D建模功能和涵盖全面物理范围的仿真求解器,Simcenter3D可以帮助您更好地了解产品的整体性能。这是通94、过一个完全集成和管理的开放环境实现的,在这里您可以对来自Simcenter和第三方求解器的任何来源的CAD数据执行所有CAE前和后处理。通过数字线程,工程师和分析师可以在一个容纳功能性能的所有方面的平台上协作。44西门子数字化工业软件白皮书 Simcenter电驱动系统性能开发Simcenter STAR-CCM+SimcenterSTAR-CCM+是目前全球最主流的商业CFD仿真软件,广泛应用于地面交通、航空、船舶、能源、化工、电子等多个行业。SimcenterSTAR-CCM+在核心的CFD仿真的基础上,集成了电磁、电化学、化学反应及结构力学等多物理场求解器,解决复杂的跨学科工程问题。Si95、mcenterSTAR-CCM+是一款高度集成化的软件,前处理、网格剖分、边界条件设置和后处理等都在统一的界面下完成,操作便捷,非常易于实现仿真流程自动化;具有先进的网格剖分功能,适用于复杂几何模型的处理和网格自动生成;无限并行求解能力,可以充分调用硬件计算资源,缩短计算耗时,具有非常好的并行计算加速比。Simcenter SPH FlowSimcenterSPHFlow是一款快速无网格计算流体动力学(CFD)软件,为设计师和分析人员提供了一个完全集成的工作流程,可以在开发周期的早期轻松快速地改进他们的设计。它采用了创新的光滑粒子流体动力学(SPH)方法。SPH方法是新一代数值方法的一部分,它96、是为了克服传统方法的网格相关约束而发展起来的,同时仍然基于Navier-Stokes方程。由于其拉格朗日特性和基于粒子的方法,SimcenterSPHFlow特别适合于高动态流动、可变形和复杂的边界和带有碎片/重连接的界面。SimcenterSPHFlow包括一个完全集成的仿真环境(SimcenterSPHFlowStudio),它为自动几何准备、仿真设置和解决方案分析提供了直观的引导用户界面。它们一起加速了涉及高度动态流体流动和运动的复杂应用程序的分析。45西门子数字化工业软件白皮书 Simcenter电驱动系统性能开发Simcenter Flotherm(XT)SimcenterFloth97、ermXT是一款以CAD为中心的电子冷却模拟软件,可以连接MCAD和ECAD工作流程,通过热分析显著缩短热设计过程。基于SimcenterFlotherm的DNA,机械工程师和热专家可以在为电子热分析设计的直观界面中轻松处理和修改本地CAD几何,以进行准确的CFD研究。稳健的EDA数据导入过程与PCB热建模的建模保真度选项相结合,包括铜痕迹焦耳加热。设计以散热器、风扇、TECs或液冷为特征的电子热管理解决方案的工程师可以消除模型创建中的典型开销,并利用参数研究来更快地优化设计。46西门子数字化工业软件白皮书 Simcenter电驱动系统性能开发Simcenter FloEFDSimcenter98、FLOEFD软件将CFD模拟的力量掌握在您的手中。在NX,Creo,CATIAV5或SolidEdge中直接使用它,以便快速探索您的想法的全部潜力,而不会中断您的设计过程。轻松了解几何形状或边界条件的变化对结果的影响,进行快速和频繁的假设分析,并在您的CAD平台中生成有见解的报告。基于智能、快速和准确的技术,SimcenterFLOEFD可以帮助减少75%的整体模拟时间,并将生产率提高40倍。Simcenter Testlab/Simcenter SCADASSimcenterTestlab是基于测试的工程的完整集成解决方案,将高速多物理数据采集与全套集成测试、分析和建模工具相结合,以满足广泛99、的测试需求。该软件旨在提高个人用户和整个团队的效率,通过在易用性和工程灵活性之间提供适当的平衡,并通过模拟关闭循环,为面向未来的测试部门提供支持。SimcenterTestlab显著地提高了测试设施的生产力,交付了更可靠的结果,即使在原型的可用性显著降低的情况下。SimcenterSCADAS硬件包括手持解决方案、紧凑和便携式移动单元、自主智能记录仪和高通道数实验室数据采集系统。依靠SimcenterSCADAS硬件的灵活性、性能和精度来执行广泛的多物理测量活动。任何SimcenterSCADAS硬件都支持各种模拟和数字换能器,用于声学,振动和耐久性工程。该硬件与SimcenterTestla100、b无缝集成,可加速测试设置并获得准确的测试结果。47西门子数字化工业软件白皮书 Simcenter电驱动系统性能开发HEEDSHEEDS的多学科设计探索和优化功能使工程师能够在包含各种来源信息的环境中进行广泛的参数研究,从而深入探究其设计仿真模型。所有这些都可以在高效搜索算法的支持下,通过优化使用所有可用资源来实现。通过这种方法,工程师可以在很短的时间内发现新的设计,优化产品性能,提高设计鲁棒性。HEEDS可以以半自动的方式,高效、安全地分析探索数百种设计方案,从而在满足约束条件的前提下实现多个性能指标间的平衡。48西门子数字化工业软件白皮书 Simcenter电驱动系统性能开发上述讨论描述了101、一个典型的电驱动设计过程。设计任务、软件要求及其解决方案在电驱动设计V型周期结合前面介绍的工程、计算和仿真挑战的背景下介绍。随着仿真方法和工具的进步,电磁,CFD,结构仿真,以及系统仿真工具使用,多目标优化算法的进步,代理或降阶模型开发,最重要的是不同工具之间的连接,这些正在形成应对电驱系统性能开发的新模式。图39总结了Simcenter的电驱动走向一体化设计解决方案。西门子的Simcenter仿真工具的开发愿景是让用户能够实现他们选择的仿真驱动设计范例。这些工具包含各种保真度级别的多个建模和分析选项,可支持高性能计算,具有开放性和可扩展性,并包含最先进的技术,可实现创新、高效计算、稳健设计、102、多目标优化等。最后,它保持了工业4.0技术在为电驱动创建终极综合数字孪生方面的核心作用。这些工具的四个核心方面是:1)前置工程,允许在设计的早期阶段集成设计流程的多个利益相关者(系统级、电磁设计和分析、热和结构工程师),2)创成式工程,使用户能够利用Simcenter有效、快速地缩小设计选择范围,3)基于模型的工程,这使得大部分设计过程都基于仿真,而不是昂贵的物理原型,以及4)连续工程,利用工业4.0技术的新发展为电驱动系统创建终极数字孪生,以帮助实施全生命周期管理的新范式。总结图39Simcenter电驱动设计解决方案西门子数字化工业软件 通过西门子Xcelerator 开放式数字商业平台的软件、硬件和服务,帮助各规模企业实现数字化转型。西门子数字化工业软件和全面的数字孪生可助力企业优化设计、工程与制造流程,将创新想法变为可持续的产品,从芯片到系统,从产品到制造,跨越各个行业,创造数字价值。了解更多,请扫码关注微信公众号西门子数字化工业软件 2023 Siemens。可在此处查看相关西门子商标列表。其他商标属于其各自持有方。业务咨询,欢迎拨打中文热线:400 120 0052(工作时间:9:00-17:30)添加企业客服微信 1058 9448林文胜180 3075 7805谢沛莘137 2872 2913董宇186 4132 6783